In 2020, 3D printed shoes are standing on firm ground. Learn how greatly 3D printing has impacted the footwear industry.
In the past decade, additive manufacturing has greatly influenced many industries, and the shoe industry is no different. The continuing advancements in 3D printing technologies enable the development of new solutions that look to be transforming the fashion and shoe industry.
While we’re still a relatively long way from 100% 3D printed shoes, there are plenty of big brands working towards mass production via additive manufacturing. With the help of innovative 3D printing players like Carbon and Formlabs, brands like Adidas and New Balance are becoming more and more successful.
Individual design companies, on the other hand, are using 3D printing to create uniquely-designed footwear or even special individual components for shoes and foot apparel.
As of today, 3D printing is no longer restricted to high-performance athlete’s shoes and those willing to pay thousands for their footwear. In this article, we’ll discuss how additive manufacturing has the potential to impact the shoe industry. We’ll then take a look at the most innovative projects and products already available to the public, from sneakers to performance shoes.
3D Printing's Potential

A Bit of History
For most of its history, the shoemaking craft was done entirely by hand. By their nature, shoes are intricate items, and traditionally, they were very time-consuming to manufacture.
Shoemaking first started to change in the 1850s, with Lyman Blake’s shoe stitching machine and Jan Matzeliger’s lasting machine. These advancements led to a new industrial approach to shoemaking, enabling mass-production manufacturing.
Today
3D printing is well-established for prototyping, and it’s only natural for the technology to be used during product development in the shoe industry. However, considering all its capabilities, it’s clear that additive technologies can have an even greater role in the shoemaking process.
Mass-customization is possibly the most exciting contribution of 3D printing to the shoe industry. Custom-made products aimed for ergonomics and exclusivity are now possible thanks to additive manufacturing processes. Just think how awesome it would be to have a unique pair of brand-name shoes specifically designed for your comfort!
With the development of new techniques and materials, the possibilities are virtually endless. In the next sections, we’ll cover some exciting projects and products that show how 3D printing is being incorporated into the footwear industry.
Running & Trail Shoes
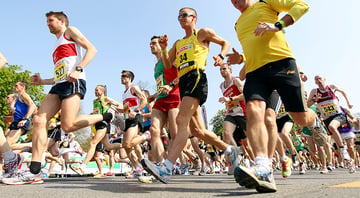
Running shoes: everyday wear for some, a place of innovation for others
Sports shoes call for extra requirements: optimal foot control, stability, and durability. These can be achieved by sophisticated design and the right choice of materials, both of which are core strengths of 3D printing.
In addition, with the help of 3D scanners, it’s already possible to produce custom-fitted shoes for professional sportspeople. This not only increases the athlete’s control in the field but also allows shoes to be constantly adjusted.
For all these reasons, huge sport apparel companies like Adidas and Reebok are investing plenty of time and money into 3D printing development for sports shoes. Below, we’ll show you some of their off-the-shelf products that have 3D printed components.
Adidas
Adidas is probably the most-engaged company in 3D printing for shoemaking. A few years back, the company partnered with Silicon Valley startup Carbon to use its digital light synthesis (DLS) technology for midsole manufacturing. This partnership has enabled Adidas to launch its first commercial release of 3D printed footwear, the Futurecraft 4D.
The shoe’s midsole lattice geometry provides different levels of pressure for the wearer. The remaining parts are still made with the regular fabric used in traditional manufacturing methods.
Adidas has ambitious plans for 3D printing and shoemaking. Since the first release of the Futurecraft 4D, the German company has launched even more products with printed midsoles, like the Y-3 Runner 4D and the new Alphaedge 4D. In 2019, Adidas also redesigned its Ultra Boost series to include the Futurecraft midsoles.
Columbia Montrail
Another sportswear giant, Columbia has stepped into 3D printing footwear with a new set of trail running shoes. The company claims they’re specifically designed for elite athletes and trail runners and it comes in three models:
- Men’s Rogue FKT II
- Women’s Trans Alp FKT II
- Fluidflex XSR
All of these models have a special 3D printed cage that’s said to make for “a seamless and glue-less construction, ensuring lightweight and secure support at all times.”
Although 3D printing isn’t extensively used in these models, this does represent an intelligent way of using the technology.
Reebok
In 2016, the American company Reebok announced a partnership with material provider BASF to develop a new concept in shoemaking: the Liquid Factory. The idea is mainly to replace the traditional molds used for making shoe parts with 3D printing techniques.
In the same year, Reebok released a limited batch of 300 shoes with 3D printed outsoles. Now, with their new Rhode Island factory, Reebok can 3D print shoe parts at a much greater scale.
Reebok’s Liquid Speed running shoe’s outsole is made out of a urethane-based liquid developed by BASF specifically for this application. According to Reebok’s Bill McInnis, this outsole design helps “create the first-ever energy-return outsole, which performs dramatically better than a typical rubber outsole.”
In 2018, the company introduced the new Liquid Floatride Run, a new model that uses the same 3D printing technology. For this model, however, the laces are the component replaced with a 3D printed structure, rather than the outsoles. The result is a stretch-to-fit slip-on shoe.
Casual Wear Trainers
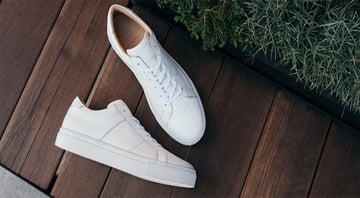
Trainers aren’t just shoes. For most, they’re a lifestyle. Whether it’s a pair of Kanye West shoes, Yohji Yamamoto, or New Balance, all of these shoes have one thing in common: They differ from conventional shoes on the market.
Producing shoes with 3D printing processes offers the possibility to design, individualize, and ultimately customize and create the most unusual structures. Below, we’ve selected the most interesting of these models, projects, and services.
New Balance
Sportswear company New Balance partnered with Formlabs in 2017 to develop high-performance materials and manufacturing processes for footwear. They came up with a new platform, called TrippleCell, which would enable the production of custom lightweight shoe parts.
This partnership resulted in the development of new material, the Rebound Resin, which is specifically designed for printing lattice structures with the same durability and longevity of their injection-molded counterparts.
This material development was followed by the redesign of the classic New Balance 990 Sport sneakers, which now feature a 3D printed heel that’s 10% lighter while maintaining the same cushioning experience.
In September 2019, the company announced its second “3D printed” sneaker model, the FuelCell Echo Triple. It uses the same Rebound Resin from Formlabs, but in this model, the 3D printed lattice structure is located at the forefoot of the shoe.
Ecco
In 2015, Danish footwear brand Ecco partnered with several companies, including material supplier Dow and software company Dassault Systèmes, to created the Quant-U customization project.
This first-of-its-kind service uses biomechanical data acquired via 3D scanners to produce highly-customized silicone midsoles aimed at increasing the wearer’s comfort. The process goes like this:
- Wearable sensors and 3D-scanning technology are used to gather the user’s biomechanical data.
- The data is interpreted and the final midsole form is obtained by generative design.
- The midsole is 3D printed using special liquid silicone rubber, after which it’s inserted into the purchased Ecco shoe.
The entire process is done in-store and takes less than an hour. While it started as an experimental project, the full service is now available at W-21, an Ecco concept store located in Amsterdam.
Wiivv
Canadian start-up Wiivv also focuses on the shoe customization business. The company provides completely custom-made 3D printed insoles and sandals. The major difference from Ecco’s Quant-U project is that the data is gathered by the own wearer through a smartphone app.
That’s right! Once the purchase is made, the Wiivv app guides the user into digitizing their feet. All that’s required is a piece of blank white paper and bare feet, of which photos are taken. The data is then processed and each foot is mapped with “over 200 points to create a 3D-printable file that is unique to each foot.”
The customer receives the finished product at home, and if they don’t fit as expected, they can be sent back for a full refund.
Fashion & Haute Couture
As is often the case with new technologies, fashion was one of the first areas into which 3D printed shoes stepped.
Let’s take a look at some of the most interesting and significant entries in the world of 3D printed shoe fashion.
Elegnano (Kathrien Herdewyn)
A few years ago, there was a big boom in the fashion industry regarding 3D printed shoes. The Belgian designer Kathrien Herdewyn, whose passion is shoe design, founded the footwear company Elegnano, which combines traditional craftsmanship with modern 3D printing.
Together with i.Materialise, she realized some very interesting 3D printed shoes, which she had tried to design as individually and uniquely as possible.
Iris Van Herpen
The designer Iris Van Herpen is known for her 3D printed fashion creations. In 2013, she presented very exquisitely designed 3D printed shoes. Although Van Herpen has since stopped producing 3D printed shoes, she has just recently made headlines with a 3D printed dress used by Joey King at the 2020 Golden Globes award festival.
Continuum
The American studio Continuum seems to be the only one out there seriously working on the design of individual 3D printed shoes. Their “Strvct” high heel is made of nylon and can keep a delicate structure while remaining light and stable – all thanks to 3D printing.
In addition, the shoes have a synthetic rubber on the bottom to provide traction. Since the designs are digitally generated, an infinite number of shoe varieties is possible.
Another project designed by Continuum is the “Myth” collection. Each shoe design can be created (for the most part) on a conventional desktop 3D printer. It was particularly important for the studio to reduce manual finishing work to a minimum in order to meet the goal of having an almost finished shoe straight off of the printer.